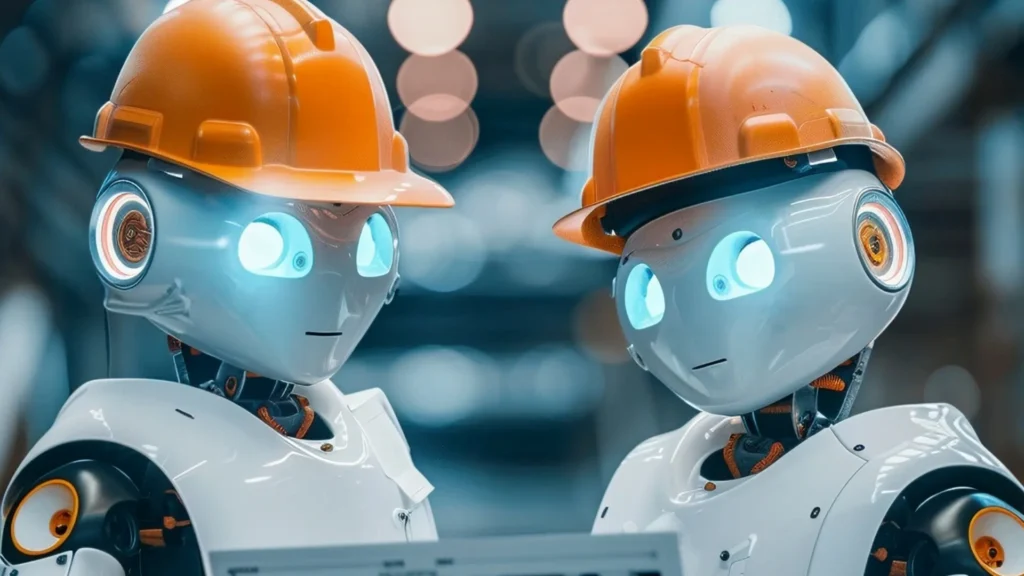
Digital Twins in Smart Manufacturing
The manufacturing industry is undergoing a massive transformation, driven by advancements in technology like the Internet of Things (IoT), artificial intelligence (AI), and big data analytics. At the heart of this revolution is the concept of digital twins—a virtual replica of physical assets, processes, or systems. Digital twins are playing a pivotal role in smart manufacturing, enabling businesses to optimize operations, reduce costs, and improve efficiency. In this blog, we’ll explore what digital twins are, how they work, and their transformative impact on smart manufacturing.
What Are Digital Twins?
A digital twin is a virtual model that mirrors a physical object, machine, or system in real-time. It uses sensors, IoT devices, and data analytics to collect and analyze data from the physical counterpart, providing insights into its performance, condition, and behavior.
For example, a digital twin of a manufacturing machine can simulate its operations, predict maintenance needs, and identify potential failures before they occur. This allows manufacturers to make data-driven decisions and improve overall efficiency.
How Digital Twins Work in Smart Manufacturing
Digital twins rely on a combination of technologies to function effectively:
- IoT Sensors: These devices collect real-time data from physical assets, such as temperature, pressure, and vibration.
- Data Analytics: Advanced algorithms analyze the collected data to identify patterns, anomalies, and trends.
- AI and Machine Learning: These technologies enable predictive analytics, allowing digital twins to forecast future outcomes and recommend actions.
- Cloud Computing: Digital twins often operate on cloud platforms, enabling seamless data sharing and collaboration across teams.
By integrating these technologies, digital twins create a dynamic and interactive representation of physical systems, providing manufacturers with unparalleled visibility and control.
Key Benefits of Digital Twins in Smart Manufacturing
Predictive Maintenance
One of the most significant advantages of digital twins is their ability to predict equipment failures before they happen. By analyzing real-time data, digital twins can identify signs of wear and tear, enabling manufacturers to schedule maintenance proactively.
For example, a digital twin of a conveyor belt can detect unusual vibrations and alert operators to perform maintenance, preventing costly downtime.
Process Optimization
Digital twins allow manufacturers to simulate and test different scenarios in a virtual environment. This helps identify bottlenecks, optimize workflows, and improve production efficiency.
For instance, a digital twin of a production line can simulate changes in machine speed or layout, helping manufacturers determine the most efficient configuration.
Enhanced Product Quality
By monitoring and analyzing production processes in real-time, digital twins can identify defects and inconsistencies early in the manufacturing cycle. This ensures that products meet quality standards and reduce waste.
For example, a digital twin of a welding robot can detect deviations in weld quality and adjust parameters to maintain consistency.
Reduced Costs and Downtime
Digital twins help manufacturers minimize operational costs by optimizing resource usage, reducing energy consumption, and preventing unplanned downtime.
For instance, a digital twin of a factory’s HVAC system can optimize energy usage based on real-time data, lowering utility bills.
Improved Collaboration and Decision-Making
Digital twins provide a centralized platform for teams to access real-time data and collaborate on solutions. This enhances decision-making and ensures that all stakeholders are aligned.
For example, engineers, operators, and managers can use a digital twin to analyze production data and make informed decisions together.
Real-World Applications of Digital Twins in Manufacturing
Siemens: The company uses digital twins to simulate and optimize its manufacturing processes, reducing production time and improving quality.
General Electric (GE): GE employs digital twins to monitor and maintain its industrial equipment, such as wind turbines and jet engines.
Tesla: Tesla uses digital twins to simulate vehicle production and optimize its assembly lines.
The Future of Digital Twins in Smart Manufacturing
As technology continues to evolve, the role of digital twins in smart manufacturing will only grow. Future advancements in AI, IoT, and 5G connectivity will enable even more sophisticated and real-time applications.
For example, digital twins could be used to create entire virtual factories, allowing manufacturers to design, test, and optimize production systems before implementing them in the real world.
Conclusion
Digital twins are revolutionizing smart manufacturing by providing real-time insights, optimizing processes, and enabling predictive maintenance. As manufacturers embrace this technology, they can achieve greater efficiency, reduce costs, and improve product quality.
The future of manufacturing lies in the seamless integration of physical and digital systems, and digital twins are at the forefront of this transformation. By leveraging this powerful tool, manufacturers can stay competitive in an increasingly digital world.